Preparation
For this week, I am going to design a stool that consists of three parts: two legs and one seat. The parts will be fixed together by press-fit.
The CNC machine that will be usesd is the Shopbot and the material will be MDF wood. The drill size is 0.25 inches and the thickness of the material will be 0.75 inches.
Design
Joints
One thing to consider about press-fitting parts together is that CNC machines cannot make right angle inside corners as the drill is round. The easy way around this is by removing extra material and creating "dog bones" joints. The figures below illustrate the issue and the solution behind it. (note: the dog bone circle diameters have to be equal to or larger than the bit's diameter)
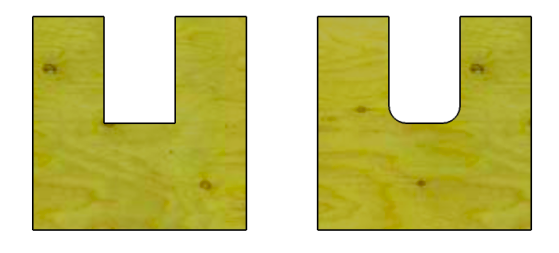
source
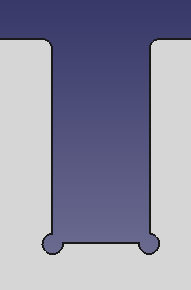
FreeCAD
FreeCAD was uses to design all of the parts. One problem that I have faced in the design phase is that FreeCAD was taking an EXTREMELY long amount of time to do any step especially the ones that were related to constraints. Some of them would even take more than 30 minutes to process. Other than that, everything else went smoothly.
The figures below are the final model parts.
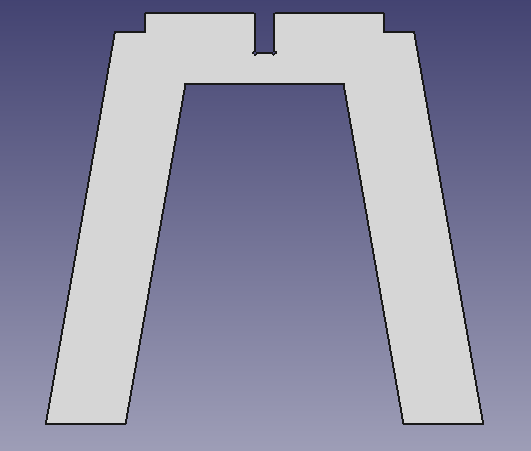
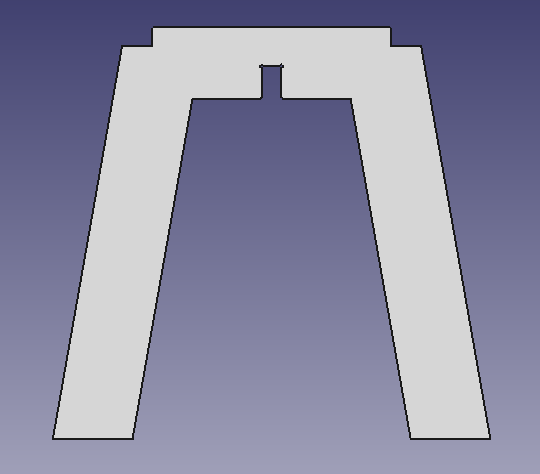
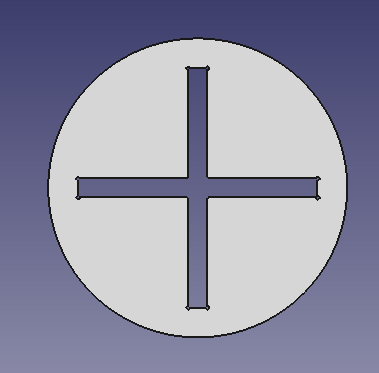
Exporting
The parts were first exported one by one as dxf from FreeCAD.
Then the files were imported into inkscape.
The three drawings were then arranged (in inkscape) in a way that there will be a balance between saving material and avoiding short distances between each part. If the distance was made small, there will not be enough material to support the mill. These parameters were not made by measurents, only by judgement.
The figure below is a screenshot the final dxf file.
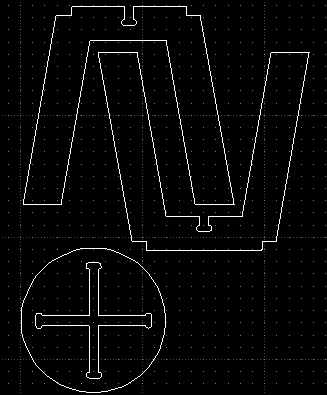